Engineered Equipment
Plating Resources has an in-depth background across several vital engineering disciplines. This diversity allows us to optimize both the plating equipment and the electrochemical processes to produce deposits of the highest quality standards. This expertise includes turn-key system design, specialized chemistry and robust equipment components that exceed all environmental and worker safety requirements. Whether you need a specific piece of equipment or a complete plating line, Plating Resources has the background needed to surpass your expectations.
Plating Systems
Our team of talented equipment engineers and electrochemical specialists design plating systems that are functional, reliable and produce high quality deposits. Our custom designed systems will exceed your production requirements while also providing future growth.
We can also revamp existing systems to adopt the latest technological innovations. Whatever the need, Plating Resources stands ready to design and install a new plating system or upgrade an existing one.
Our engineered systems protect vital environmental resources – air, water, and land while also protecting your workforce. A properly designed system produces air discharge testing far below the Chromium Plating NESHAP 40 CFR Part 63 Sub Part N EPA Regulation. Data from a recent project resulted in a ‘no detectable Cr’ discharged during stack testing. Air sampling showed the plating workers were between 55 – 156 times below the OSHA Hexavalent Chromium PEL standard. In addition, the shop stayed clean and free of mist build-up.
These tests confirm a properly designed system can surpass the EPA and OSHA regulations by a wide margin. Expensive fume suppressants are not needed with our Sustainable Technology.
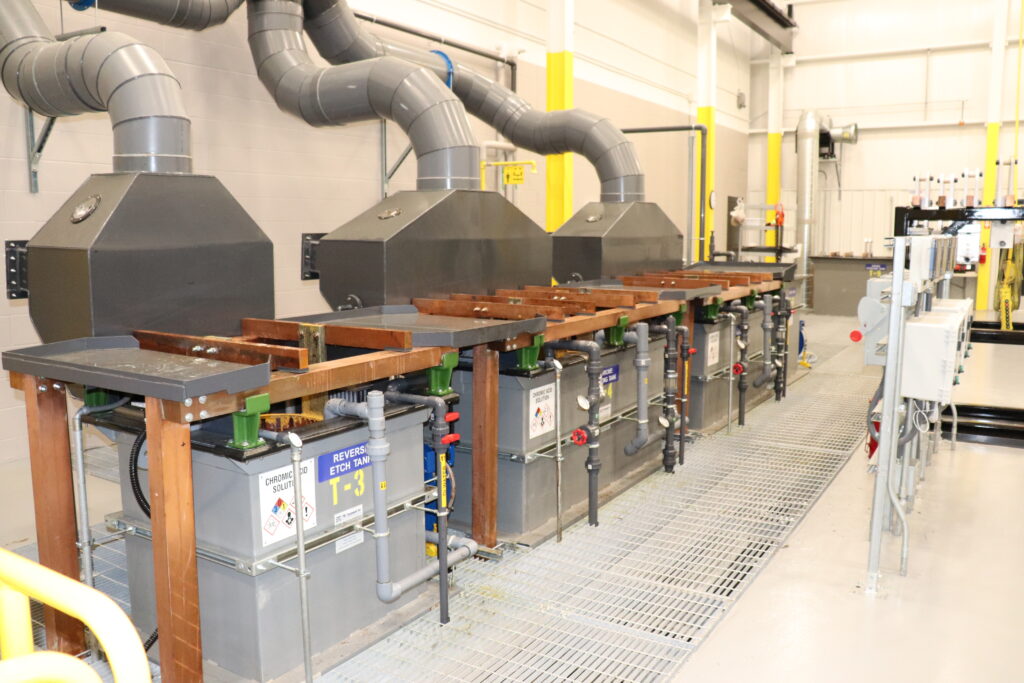
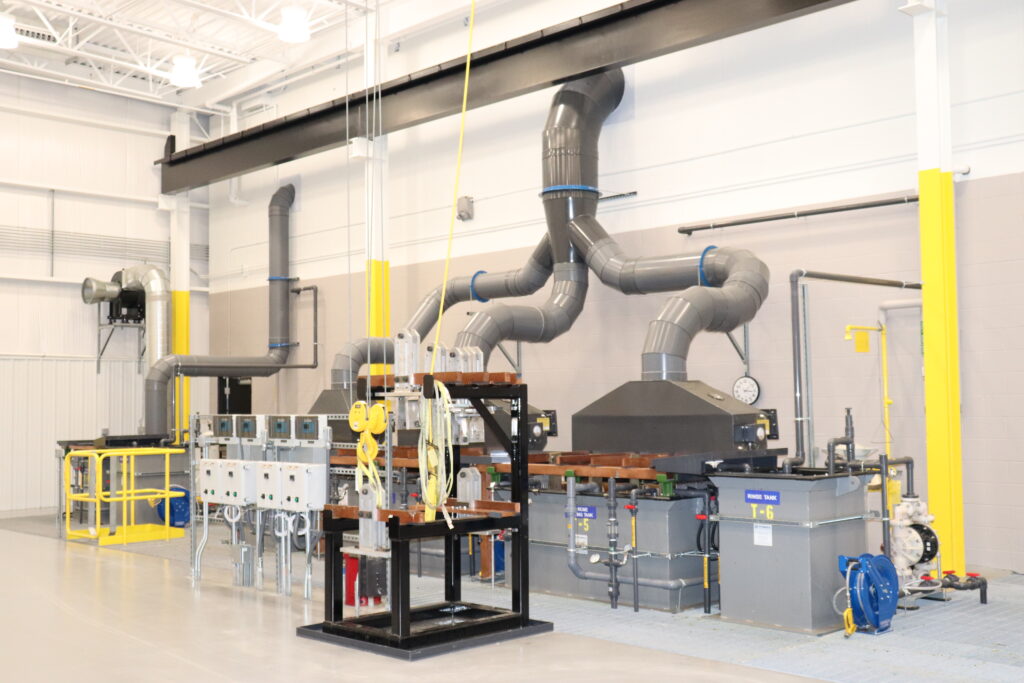
Zero Discharge Recovery
Our plating systems are designed to capture and reuse all rinse water, ventilation wash-downs and any splashes or spills that may occur. Zero Discharge Recovery significantly lowers your operational costs by recycling and reusing all process chemicals. There are no sewer connections whatsoever with our Zero Discharge design and expensive waste treatment systems are not needed.
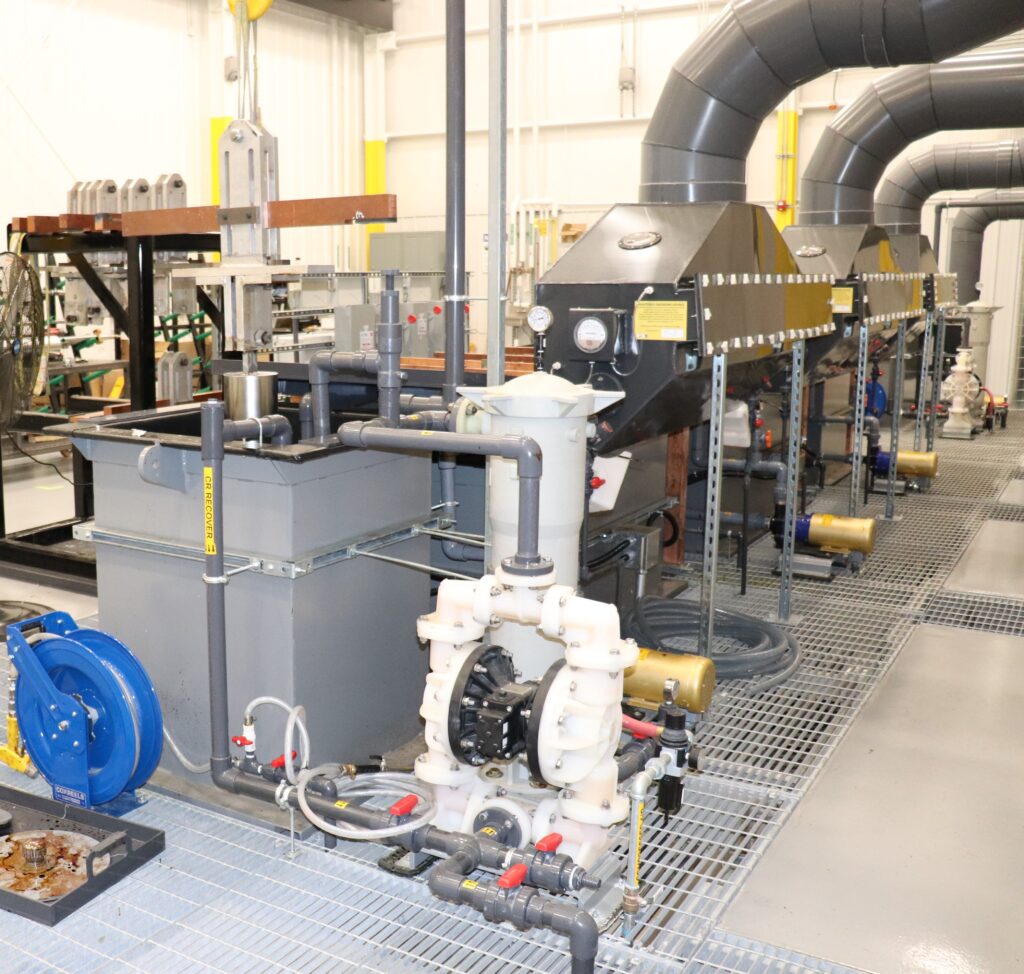
Zero Discharge Rinsing
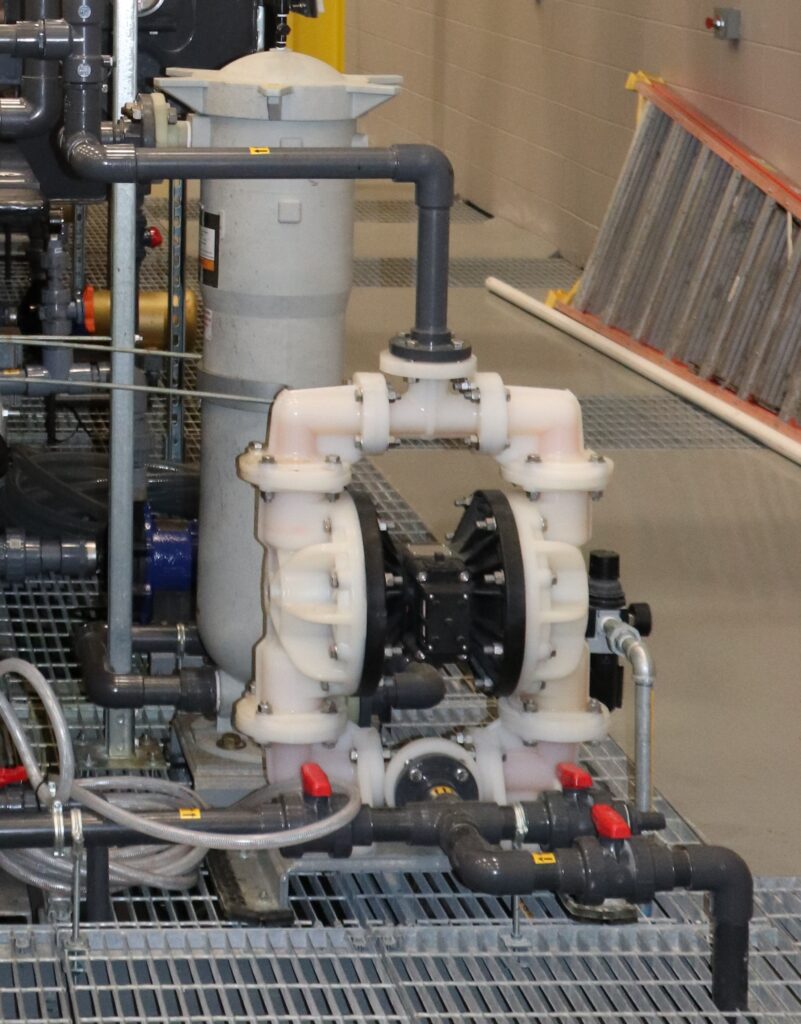
Zero Discharge Recovery Units
Ventilation
Ventilation systems are a key component in protecting your workforce and the environment. When operated properly, they yield results well below the EPA and OSHA regulations.
Our ventilation systems are sized to exceed the OSHA requirement of 250 CFM per sq ft of plating tank surface area. This design consists of multiple mesh pads to entrap any chromium laden mist and a HEPA filter before the airstream discharges to the outside atmosphere.
The ventilation system includes test ports necessary to conduct the stack test to comply with the Chromium Plating NESHAP 40 CFR Part 63 Sub Part N EPA regulation. The system design is so efficient that stack testing indicated ‘No Detectable Cr Discharge’, i.e.: essentially Zero.
When designing the ventilation system one of the areas we consider is the washdown of the mesh pads. The flow rate and the frequency of the mesh pad washdown is calculated based on the evaporation rate of the process tanks. By doing so, the washdown water can be fully reclaimed without additional equipment or generating hazardous waste. These design criteria and features ensure your employees and assets are protected while reducing your liability.
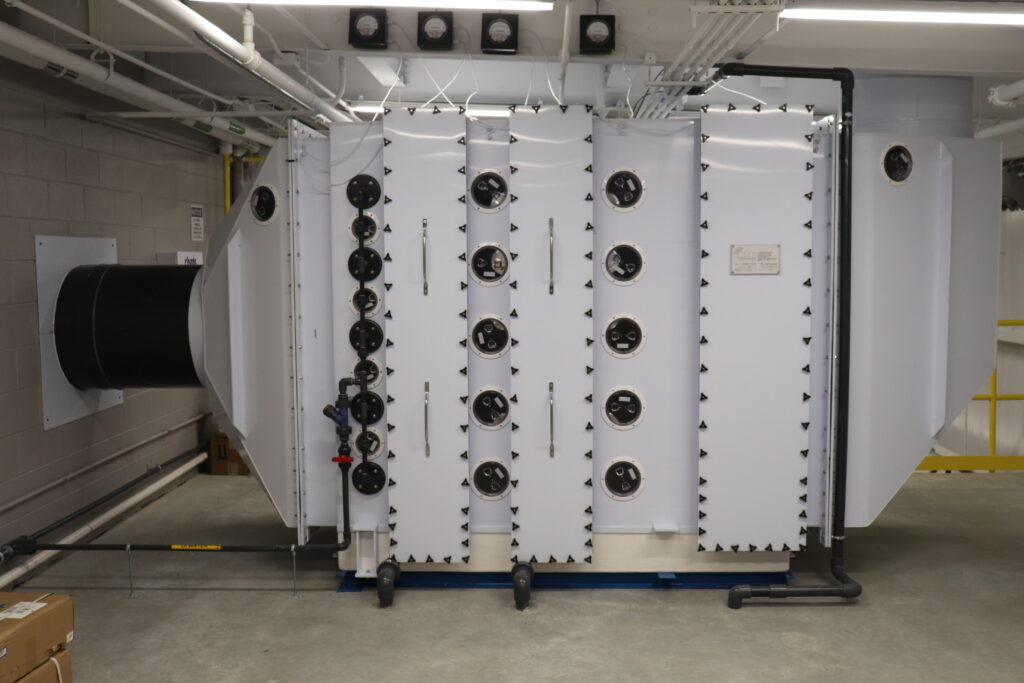
Mesh Pad Eliminator with HEPA Filter
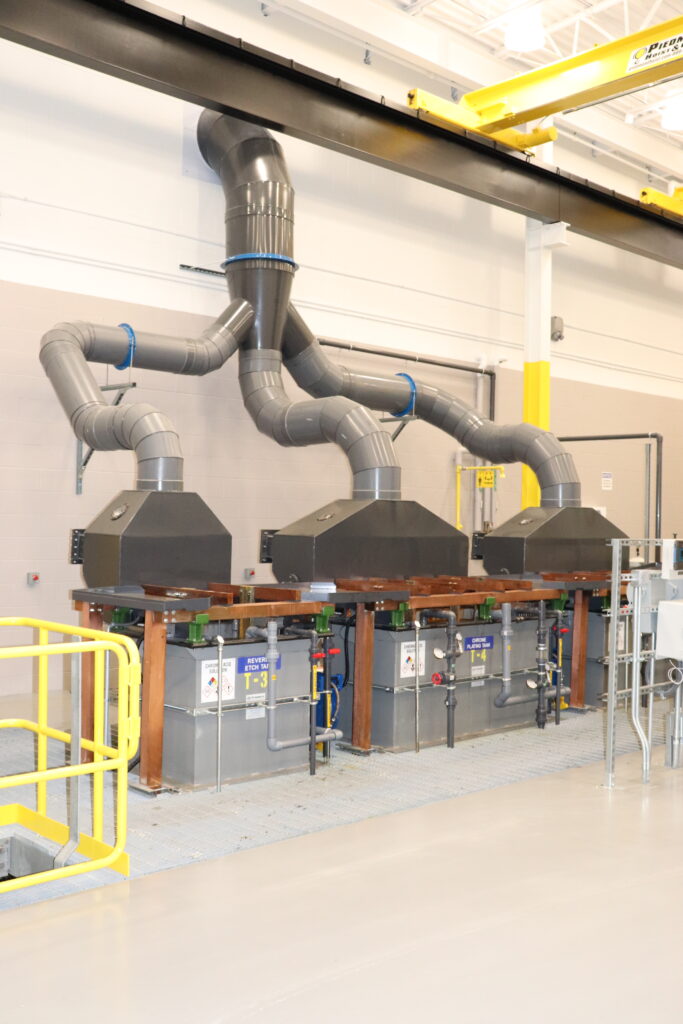
Engineered Ventilation System
Rectifiers
Rectifiers convert an oscillating two-directional alternating current (AC) to single-directional direct current (DC) that is required for electroplating. Plating Resources recommends and provides switch mode rectifiers over silicon-controlled rectifiers (SCR’s). There are many reasons for this recommendation. The most important is that switch mode rectifiers are highly efficient across their entire power range. Whereas, SCR’s are only efficient when operated at their full voltage. These are available in either air- or water-cooled versions with or without pole reversing and replace the outdated SCR and tap-switch type units.
Switch mode rectifiers are built in modules to virtually any amperage requirement and most are supplied in 12-volt versions, without additional cost. This higher voltage is better suited for overcoming resistance in the bussing, fixturing, anodes or the plating solution. This frequently improves the plating quality, the plating speed and the overall production quantity.
Another great feature of using a switch mode rectifier is the ripple is maintained well below 1% (typically around 0.1%) without the need for expensive choke filters. This purer DC waveform also equates to improved deposit quality and faster production.
Switch mode rectifiers are also much smaller than a comparable SCR unit would be and they are much quieter. Another great feature of these units is they come with programmable controls and timers. This makes it easy to dwell the start time, ramp-up, provide a surge current, enter a stop time and many other options that were previously done manually.
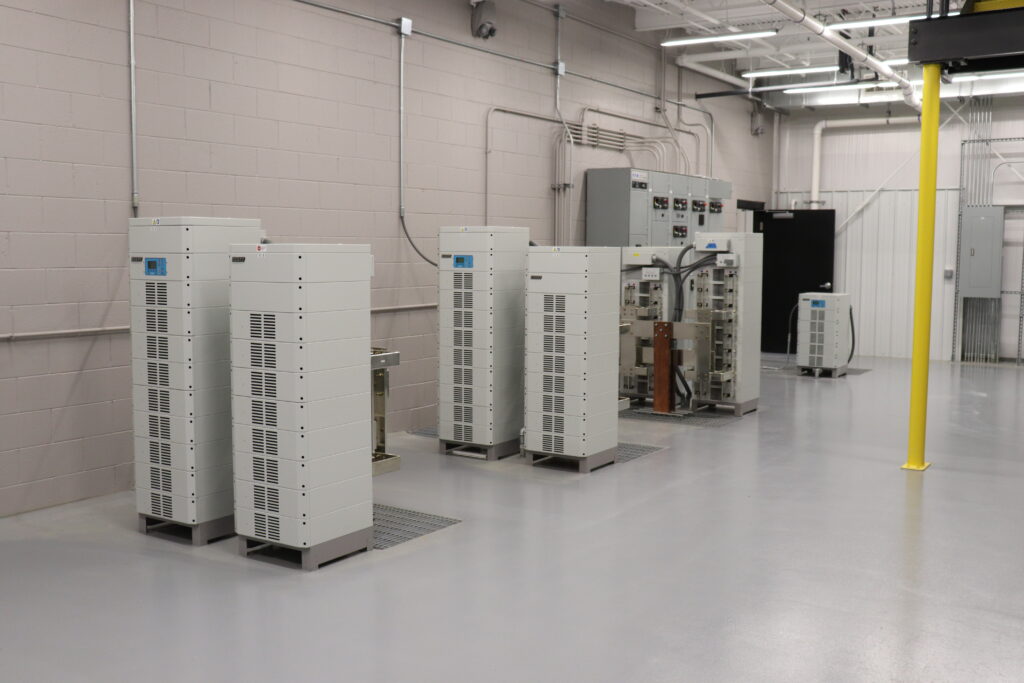
Switch Mode Rectifiers
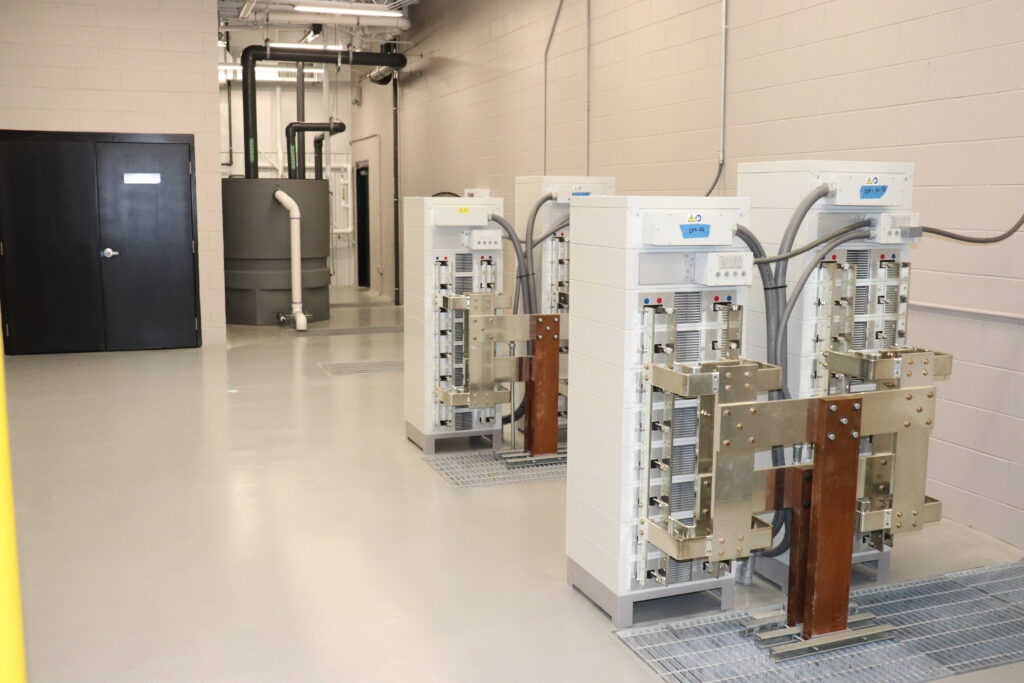
Switch Mode Bussing Connections
Tanks
A variety of tanks are needed in a plating operation. The materials of construction are selected based on the chemistry and temperature of the bath solution. Plating Resources provides engineered tanks that exceed the process requirements, are robust and provide many years of service. Some of the construction materials available include:
- Koroseal™ Lined Steel Tanks
- Stainless Steel Tanks
- Polypropylene Tanks
- Kynar Tanks
Horizontal and vertical stiffeners are used as necessary to prevent the tank walls from bulging. We also include multiple lift points in the tanks construction to allow the tanks to be safely lifted and installed.
We do not recommend using drop-in liners. They are invariably larger than the inside tank dimensions. This causes the excess material to fold and protrude away from the tank wall where it can be easily torn by an anode or cathode or come in contact with a heating element. Any of these scenarios creates a costly maintenance issue that may not be immediately evident. If not addressed, the structural integrity of the steel will become compromised. A better option is to use tanks having the correct materials of construction with the Koroseal™ liner bonded to the steel with strict adherence to the Koroseal™ procedures.
Heating and Cooling
Many process and plating baths require heating and some also require cooling. We provide both in-tank heaters and cooling coils as well as external heat exchange units that save tank space. These come with digital controls that maintain the bath temperature within 1-2° F.
Plating Anodes and Fixtures
Plating anodes and fixtures are an integral part of a functional plating system. They are vital in providing the desired deposit quality and production rate. Our experienced team looks at these factors when designing the fixtures and anodes based on the geometry of the workpiece. Our preference is conforming anodes whenever possible to insure a consistent and uniform deposit.
Our anodes for a hard chrome electroplating operation are typically manufactured using a lead alloy containing 2% Tin and 4% Antimony. It is an economical means of conducting the required current for the electroplating process without contaminating the bath as does steel anodes. Platinized titanium or MMO anodes are used where thin anodes are required due to unusual surface profiles on the parts being plated. Regardless of the workpiece geometry, we can design the appropriate fixture and anode to meet your requirements.
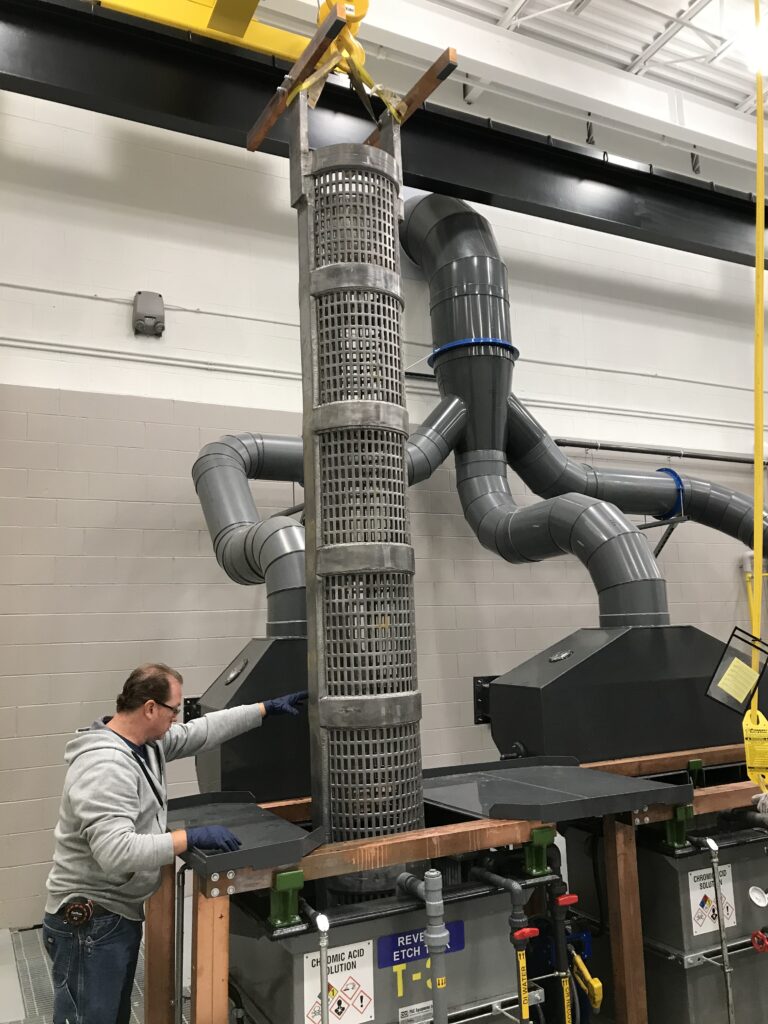
Conforming Anode
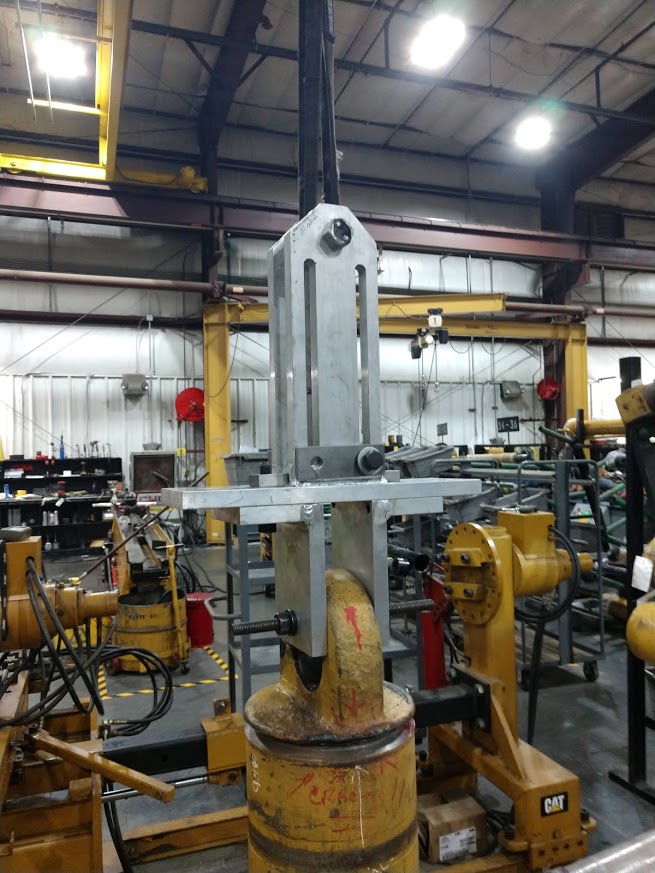
Adjustable Rod Fixture
Containment
Our systems are engineered with all the process tanks located within a containment area. The volume of the containment is larger than the total tank volumes by a significant safety margin. The containment area is segregated by chemical type so unlike chemicals are not mixed, which would otherwise create a waste product. This allows any spills to be easily reclaimed for reuse in the various processes. This containment is part of our Zero Discharge Recovery and Sustainable System design.
Each containment zone is lined with a heavy monolithic layer of fiberglass matting and the appropriate resin to withstand the chemistry. The liner bonds tightly to the concrete, is extremely corrosion resistant and is virtually indestructible. Yet, it is easily repairable if ever necessary. The containment lining protects the subsoil, the groundwater, and your property value.
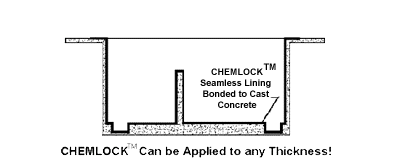
Bath Agitation
Bath agitation is needed to keep the chemistry and temperature uniform across the entire plating tank. Air agitation has been used extensively, but it has significant drawbacks. First, it creates undesirable mist products that are thrown into the plant air as the air bubbles break at the baths surface. Secondly, it has an unwanted cooling effect on the bath while possibly introducing contaminates such as lubricating oils and debris into the plating solution. The air bubbles from this type of agitation can also create a barrier to the flow of DC current which can lead to poor plating quality and slow plating speeds.
Plating Resources engineers recommend solution agitation in place of air agitation. Solution agitation is a more effective means of keeping the plating bath thoroughly mixed to ensure homogenous chemistry and temperature throughout the plating tank. Solution agitation is also more affective at replacing the cathode film with fresh solution and removing cathodic gassing.
A solution agitation system consists of a series of eductors, a pump and CPVC plumbing. The eductor consists of two elements, a nozzle with a small orifice and a diffuser with a gap between them. As the bath is pumped through the nozzle at high velocity, it pulls additional bath liquid from the surrounding gap area. The entrained fluid mixes with the pumped fluid before discharging back into the bath. The result is an agitation flow rate approximately 5 times greater than the pumped volume.
How the eductors are arranged in the plating tank is dependent on several factors. These include the size and depth of the planting tank and the geometry of the cathode. The eductors can be mounted vertically, horizontally, or at an angle. They are typically mounted by the tank wall to prevent damage from the anodes or cathodes.
Eductor agitation is typically 100 times better than air agitation is. This is because the bath interior is moving vigorously with many changeovers per hour, yet the solution surface is relatively calm.
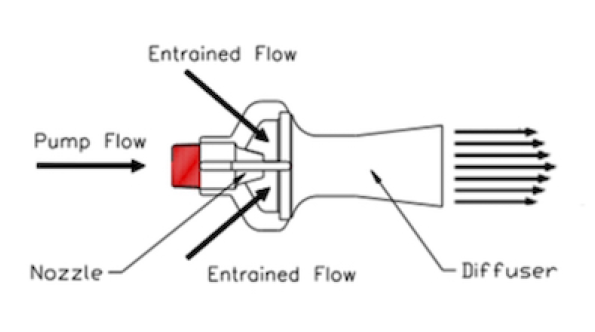
Eductor Design
(Illustration courtesy of BEX Incorporated)
The benefits of solution agitation are the following:
- It creates under-surface turbulence without inducing air into the bath causing misting at the baths surface.
- Eductors are aimed at the work piece ensuring fresh solution is always in contact with the plated surface.
- It is a closed loop system thereby preventing external contamination of the bath.